Composites forming

Shear angles during thermoforming of thermoplastic prepregs Experimental-simulation comparisons
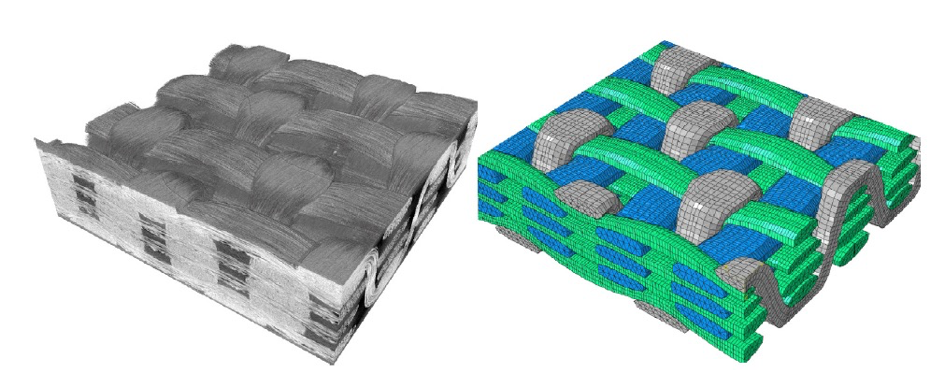
Mesoscopic analysis of 3D reinforcement compaction. Experimental-simulation comparisons
The main aim of manufacturing parts in composite materials is to reduce weight while maintaining good mechanical properties. Recently, the use of composites has grown considerably, particularly in the aeronautical industry. Projects are also underway in the automotive sector. The analysis of manufacturing processes, which are many and varied, aims to determine the conditions of feasibility and the state of the manufactured part, in particular the directions of the fibers, their volume fraction and any defects. The Multimap team at LaMCoS carries out research into the shaping of composites. The aim is to develop methods and software for simulating these composite processes. Studies are carried out at both macroscopic (part scale) and mesoscopic (elementary mesh scale) levels. Behavior laws for fibrous media undergoing major transformations are developed and identified through specific experimental tests. Beyond the hyperelastic and hypoelastic Cauchy frameworks, generalized continuum mechanics approaches are developed to take into account the local bending stiffness of fibers. The very strong temperature dependency is also analyzed for thermoplastic prepregs, where thermoforming takes place in the vicinity of melting. For this thermoforming process for thermoplastic prepregs, the analysis of consolidation is important. The porosities created by heating the prepreg must be eliminated by compaction. To this end, a prismatic solid-shell element has been developed, taking into account the transverse stress that verifies the boundary conditions on the outer surfaces of the shell. The Multimap team is developing Plasfib software to simulate composite shaping. Elements of shells, solid-shells and fibrous shells are developed. In the latter case, special kinematics are used. Kirchhoff and Mindlin kinematics are replaced by near-inextensibility of the fibers and sliding with possible friction between the fibers. The shaping of multilayer reinforcements or prepregs is one of the objectives of the simulations. The various simulation approaches are validated by comparison with forming tests.
Much of the research is carried out in collaboration with companies (Safran, Airbus, Solvay, etc.) and as part of ANR and FUI projects. Mesoscopic analyses of elementary textile meshes are aimed at numerically determining the mechanical properties (particularly compaction) and permeability of the reinforcement. Finite element models for these analyses can be obtained from X-ray tomography.
Contact : MARTOIA Florian